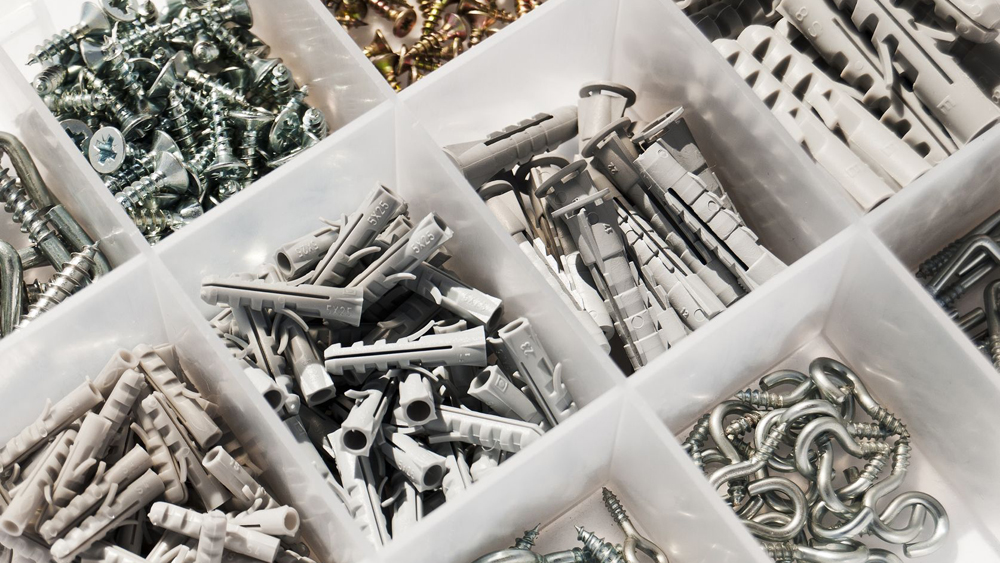
Fixings. The different methods of securely fixing and installing roller blinds.
There are various fixing and installation methods for roller blinds, each with its own set of benefits. The way your blinds are installed can affect the amount of light that comes in, the functionality of your windows and the overall design of your room.
There’s two main ways to install roller blinds;
Top Fix
This is the most frequent method used to install roller blinds. What it means is that the blind is fixed upwards into the top (Horizontal surface) of the recess. This can be used to save space as the blind protrudes less into the room however this will leave a small light gap above the roller as you can see in the image above.
Face fix
Face fix is when the blind is fitted straight to a vertical surface such as the wall over the window opening or the window frame itself. This will generally mean the fabric cover overlaps the glazes area of the window which results in less light gaps.
Different options such as black out fabric can be used to block sunlight even further. Our article on fabric types can be found here.
When fixing a roller blind it is important to take into consideration what type of substrate (wall/surface/recess) the roller blinds are getting fixed to. Even with a high quality blind system and a skilled fitter, if the substrate is not suitable you have a risk of the blind coming away from the surface it is fixed to.
Different types of fittings are available for different wall types.
- Wood
The best substrate in the opinion of most installers. On an external wall of a building, this is generally a 3 x 1 inch timber batten fitted above the window or a timber “pattress” installed behind the plasterboard. This gives a very secure fitting for any blind system using standard timber screws and is also very quick and easy to fit to for maximum efficiency during window blind installation.
- Aluminium
This would generally be when the blinds are being fitted directly into the window frame or curtain walling section. This is done using self tapping screws usually in typical lengths, specified in fractional inches, span from 3/16″ to 3 1/2″. This method would normally need to be approved by the window or curtain walling manufacturer. Provided this is approved this is also a very secure and quick way of fitting roller blinds.
- Brick
This is generally in older buildings before dry lining type plasterboard was popular. Fixing into brick is a very secure way of fixing blinds but is much more time consuming for the installer. This is because the installer first has to drill a small hole in the brick using a hammer drill and masonry drill bit before then can install the blind using necessary fixings. The fixing used for this substrate are usually red or brown plugs such as those shown in the image below and then as a general rule the length of a masonry screw must be equal to the thickness of the material being fastened plus a minimum of 1” with a maximum embedment of 1-3/4” .This method however, is likely to take around 3 times longer for an installer than fixing into aluminium or wood.
- Concrete Lintel/Blocks
Much the same as fixing into Brick. Concrete provides a very secure fixing for roller blinds but it is very time consuming.
A catnic lintel is a very thin steel section that is installed above a window opening. (Find below picture taken from their website)
Whilst steel is very hard due to this section being thin it can present a reasonable fitting option for smaller roller blinds.
This is generally done using self tapping screws (see image above) which have a small cutting piece on the end that drills through the steel ahead of the threaded section which bites into the thin steel section to secure the blind. This is less secure than the method listed above but is more secure than plasterboard. Fixing into Catnic lintel is only really suitable for small-medium weight blinds and whilst is not as quick as fitting into wood or aluminium it is quicker than brick or concrete.
- Steel
This refers to more of a general steel section which likely forms a part of the building structure. Steel is a very time consuming fixing substrate for blinds as special drill bits are required to cut through the hard surface. Whilst this is time consuming the actual fixing is secure once completed. This substrate is likely to take longer than even concrete or brick.
- Plasterboard
This is very common due to the lack of planning for a suitable roller blind fixing substrate and the popularity of dry lining type plaster board in modern construction. Whilst this substrate is popular it is probably the most challenging for an installer and has the highest risk of failure. Plaster board is both time consuming to fix to and results in a very weak fix. Fixing manufacturers have come up with a number of solutions for fixing into plasterboard. The two most common are below;
Pig Tail fixings – These are a poor solution for blinds and often fail resulting in the blind falling down.
Plasterboard fixings
These are good but require space and there is still a risk of failure as plaster board can only take limited amount of weight.
According to this article by Vcut (plasterboard supplier), SNAPTOGGLES are the most effective fixings that can be used on plasterboard.Snap Toggles require a somewhat larger hole than most other fixings – typically 12 inches – than most other fixings. The snaptoggle is then pulled back into place after being put through the hole. When the plastic connectors are flush with the wall, slide them down and snap them off; then screw in normally for a professional finish.
For more information on roller blinds or for pricing on roller blinds please contact us by clicking below.